Rail Flaw Detection
UT – RFDU
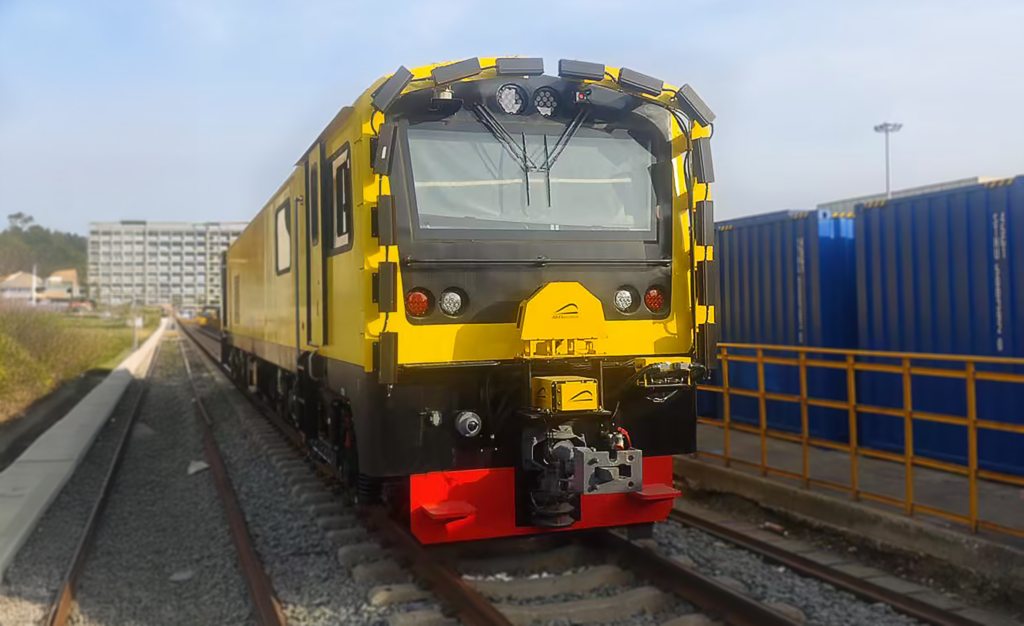
Strategic Value
The integration of these systems into a single platform enables ADTS to offer a holistic diagnostic solution to rail operators. By transforming maintenance strategies from reactive to proactive, the UT-Rail train enhances operational safety, infrastructure lifespan, and cost-effectiveness.
ADTS is proud to contribute to the future of smart railway monitoring by delivering powerful, real-time diagnostics through innovative engineering.
UT-Rail Flaw Detection Measurement Train
The UT-Rail Flaw Detection Measurement Train is a cutting-edge railway diagnostic vehicle developed to support the safety, reliability, and long-term sustainability of railway infrastructure. Specifically tailored to monitor the condition of Taiwan’s railway network, this highly specialized train integrates multiple inspection systems to perform real-time, high-precision assessments of track and tunnel conditions.
Purpose & Capabilities
The primary goal of the UT-Rail train is to enable preventive and predictive maintenance, reducing unplanned downtime and enhancing the overall safety and efficiency of railway operations. By conducting comprehensive, automated inspections at speeds of up to 60 km/h, the train ensures early detection of potential issues before they evolve into critical failures.
With a length of 22 meters, the vehicle is equipped with nine advanced diagnostic systems, each targeting specific aspects of the rail infrastructure:
System Overview
Utilizes high-resolution LiDAR and imaging technology to inspect tunnel structures. It detects deformations, cracks, and structural irregularities, providing a 3D reconstruction for engineering analysis and maintenance planning.
A high-definition video monitoring system that continuously captures visual data of the railway track. It enables operators to detect debris, obstacles, surface-level defects, and wear patterns in real time.
Employs ultrasonic waves to detect internal flaws within the rail such as fatigue cracks, inclusions, or corrosion. This non-destructive testing technique is essential for identifying subsurface anomalies invisible to the naked eye.
Assesses the geometric alignment of the track, including gauge, cant, twist, and level. Maintaining proper track geometry is critical to safe and stable train operations, especially at higher speeds.
Focuses on identifying surface-level cracks and fractures along the rail. It complements the UT system by detecting early-stage rail fatigue and stress indicators that may affect performance or lead to failures.
Measures rail surface irregularities (such as wave-like corrugation) that contribute to increased noise, vibration, and accelerated component wear. Timely detection helps maintain ride quality and reduce maintenance costs.
Captures the complete cross-sectional profile of the rail to assess wear, deformation, and dimensional consistency. Ensures compatibility with rolling stock and promotes safer wheel-rail interaction.
Inspects third rail systems used for electrical power delivery. It verifies alignment, continuity, and surface condition to prevent power interruptions or electrical hazards.
Monitors spatial clearance around the track to ensure safe passage of trains through tunnels, stations, and other restricted environments. Detects vegetation, debris, or encroaching structures.
The computer is designed with a high-speed and high-performance industrial control computer, which is installed with the core flaw detection software. It can realize user’s terminal operation control and dynamic real-time display of defect results. The whole signal processing system can meet the parallel processing of ultrasonic signals, flaw feature signal extraction, multi-channel data space conversion, data
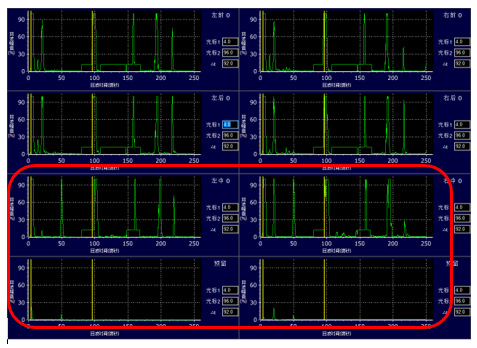