R.P. Grinder
Intelligent Rail Grinding Optimization
R.P. Grinder
is an advanced measurement configuration that integrates high-precision Rail Profile and Corrugation Analysis Systems directly onto your grinding machinery. This setup allows for real-time rail wear monitoring and precision diagnostics, ensuring the grinding process is optimized for maximum efficiency, safety, and rail longevity.
Real-Time Rail Profile Monitoring
At the core of the R.P. Grinder system is our Rail Profile Measuring System, which utilizes laser triangulation to capture the exact shape of the rail in high resolution. The system compares the current rail geometry to a reference profile, accurately identifying wear patterns and transverse deformation.
- Up to 350 fps sampling frequency
- ±0.1 mm accuracy
- Wide temperature range (-20°C to +60°C)
- Laser Class 3B (450 nm)
This allows operators to prepare grinding operations more accurately and extend the lifespan of both rail and grinding tools.
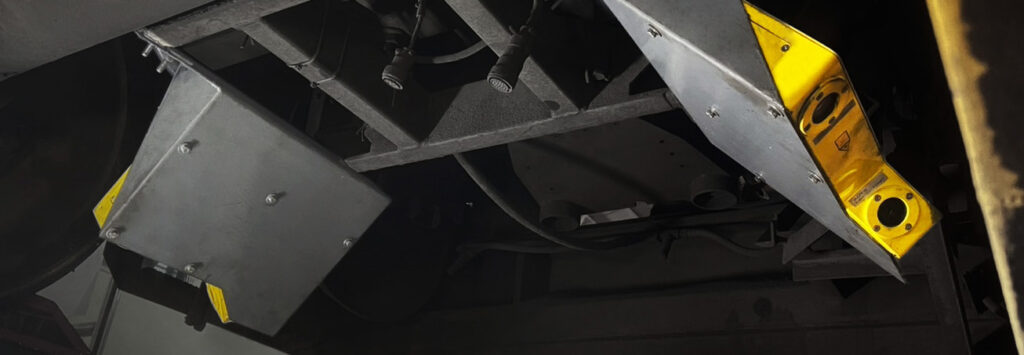
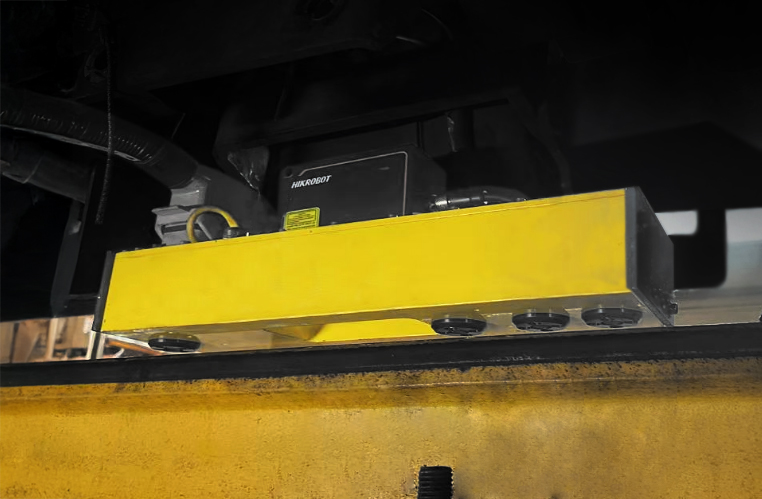
Corrugation Measurement Integration
The R.P. Grinder configuration also includes Corrugation Analysis capability—detecting fine surface defects such as short-pitch corrugations, waveforms, and noise-related anomalies that degrade ride quality and increase maintenance costs.
Mounted directly onto the grinder machine, the corrugation system:
- Measures surface roughness and wavelength
- Provides instant feedback on grinding effectiveness
- Helps track progress over time with post-process comparisons
Seamless Integration with Grinder Machines
The full system is designed to work in sync with standard rail grinding machinery. The compact sensors and robust design ensure reliable performance even under harsh working conditions—dust, vibration, and high speeds.
Operators benefit from:
- Front-facing “Machine View” mode for real-time visual diagnostics
- Thermal imaging compatibility (optional add-on)
- Integrated reporting tools and export-ready data formats
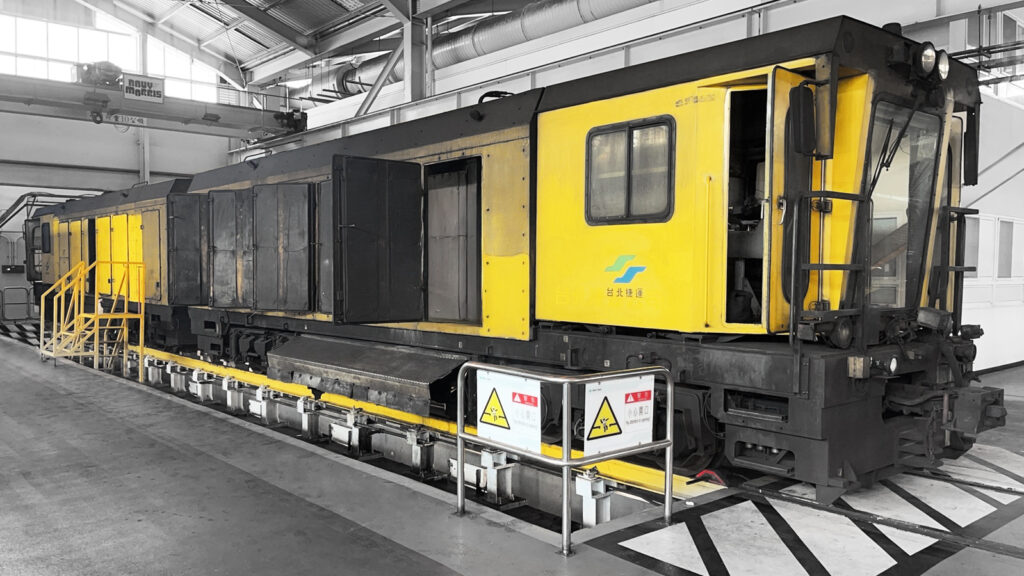