Clearance Gauge
Measuring System
Clearance Gauge Measuring System
The Clearance Gauge Measuring System developed by ADTS is an advanced, vehicle-mounted solution for high-precision clearance inspection of railway infrastructure. Installed on TRA inspection vehicles, the system performs dynamic, non-contact measurements to assess whether rail corridors comply with regulatory clearance limits.
It plays a crucial role in ensuring railway safety, by detecting over-limit structures or potential obstructions before they pose risks to train operations.
Main Components
ZF9020 Laser Profiler
A high-speed, phase-based 3D laser scanner that collects over 1 million points per second with 360° coverage. It accurately maps the environment around the track.IMU (Inertial Measurement Unit)
Monitors the motion and orientation of the vehicle to allow precise alignment of the scanned data.Encoder (Odometer)
Installed on the vehicle’s wheel to measure distance and synchronize data with position.Video Inspection System
Includes a high-definition day/night camera and infrared illuminators to visually document the inspection area.GPS System
Ensures geolocation tagging of every scanned segment for accurate mapping and reporting.Control Cabinet (Onboard)
Contains the power supply, synchronization unit, and computer hardware that run the system and manage acquisitions.
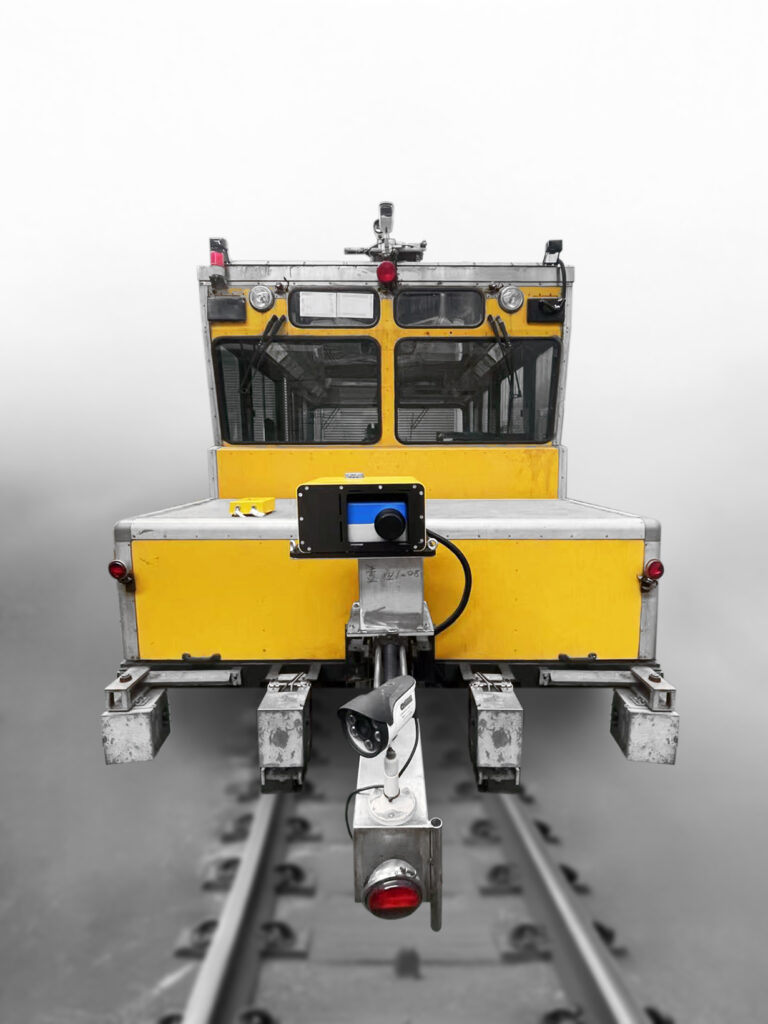
Functionality
The system compares live scans with preloaded clearance profiles (DXF format) to detect anomalies or obstructions.
The accompanying CLEARANCE software handles real-time acquisition, visualization of profiles, and system control. All deviations or over-limit areas are flagged for review.
Post-processing is performed using AHMES, a review software that allows:
Profile visualization (point cloud)
Overlay of reference profiles
Image analysis from the camera
Automatic detection and tagging of clearance violations
Generation of professional PDF reports
Safety & Maintenance
Integrated laser safety compliant with EN ISO 60825-1
Requires protective eyewear (OD 6+) and qualified personnel for operation
Regular maintenance includes:
Weekly: visual inspection and cleaning
Quarterly: full system checks and calibration
Annually: deep cleaning and hardware review
Cleaning procedures follow strict guidelines using only approved lens-safe materials like ZEISS optical fluid and lint-free tissues.